Coordinate Measuring Machine (CMM)
Use CMM laser scanning to simplify inspection processes, deliver rapid non-contact measurement and provide geometrical insight in a range of applications.
Our CMM laser scanning services are ideal for.
3D digitizing to the highest detail
3D scanning of high precision or fragile parts and complex surfaces
Creating complete 3D visualization of dimensional quality using colour mapping
Measuring and analysis of features within parts
Replacing traditional tactile probe measurement
X2 CMM Setups.
LKV 20.12.10.
Our LKV 20.12.10 machine has Renishaw ACR multi-sensor auto-changing rack allowing us to combine traditional touch probe with non-contact laser scanning effortlessly. This machine can measure single components up to 2000mm x 1200mm x 1000mm.
LKV 8.7.6.
Our LKV 8.7.6 machine has Renishaw ACR multi-sensor auto-changing rack allowing us to combine traditional touch probe with non-contact laser scanning effortlessly. This machine can measure single components up to 800mm x 700mm x 600mm.
Our Nikon Scanners Heads.
LC15Dx
Thanks to the most advanced laser scanner technology, the LC15Dx is closing the gap with tactile probe accuracy. In tests comparable to ISO 10360 the LC15Dx achieved the accuracy expected when using a CMM with a tactile probe.
XC65Dx-LS
The multi-laser XC65Dx laser scanner captures all 3D details of features, edges, pockets, ribs and freeform surfaces in a single scan. It’s entirely digital 3D digitizing operation boosts scanning frequency and drives smart laser intensity adaptation to scan any surface without user interaction.
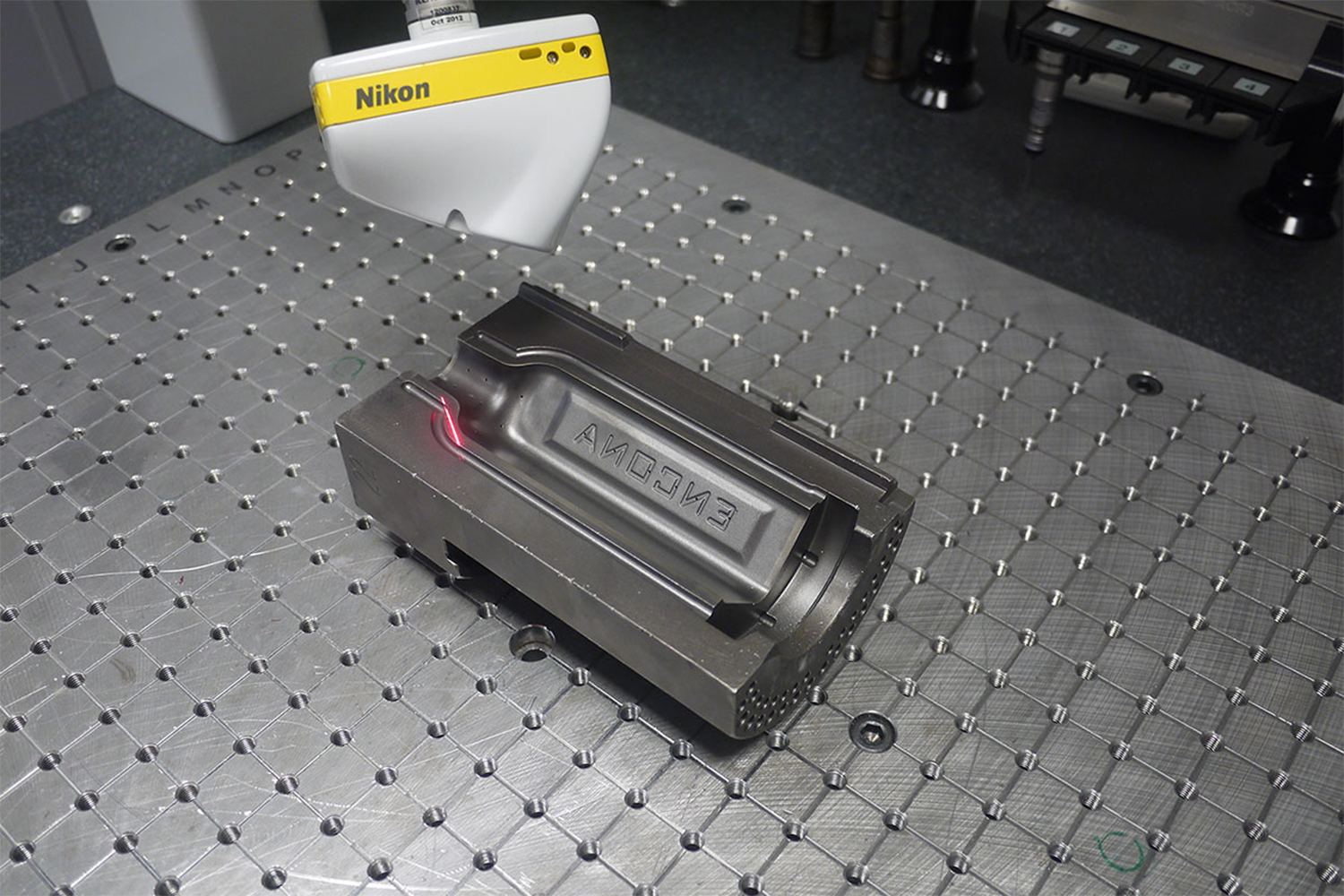
Repeat CMM Capacity.
We have the capacity and availability for repeat CMM scanning. Our expert team has a long history working within a range of industry sectors ranging from Aerospace to Medical and many more. We will work closely with your team to ensure accurate, repeatable results. Starting at £60 per hour.
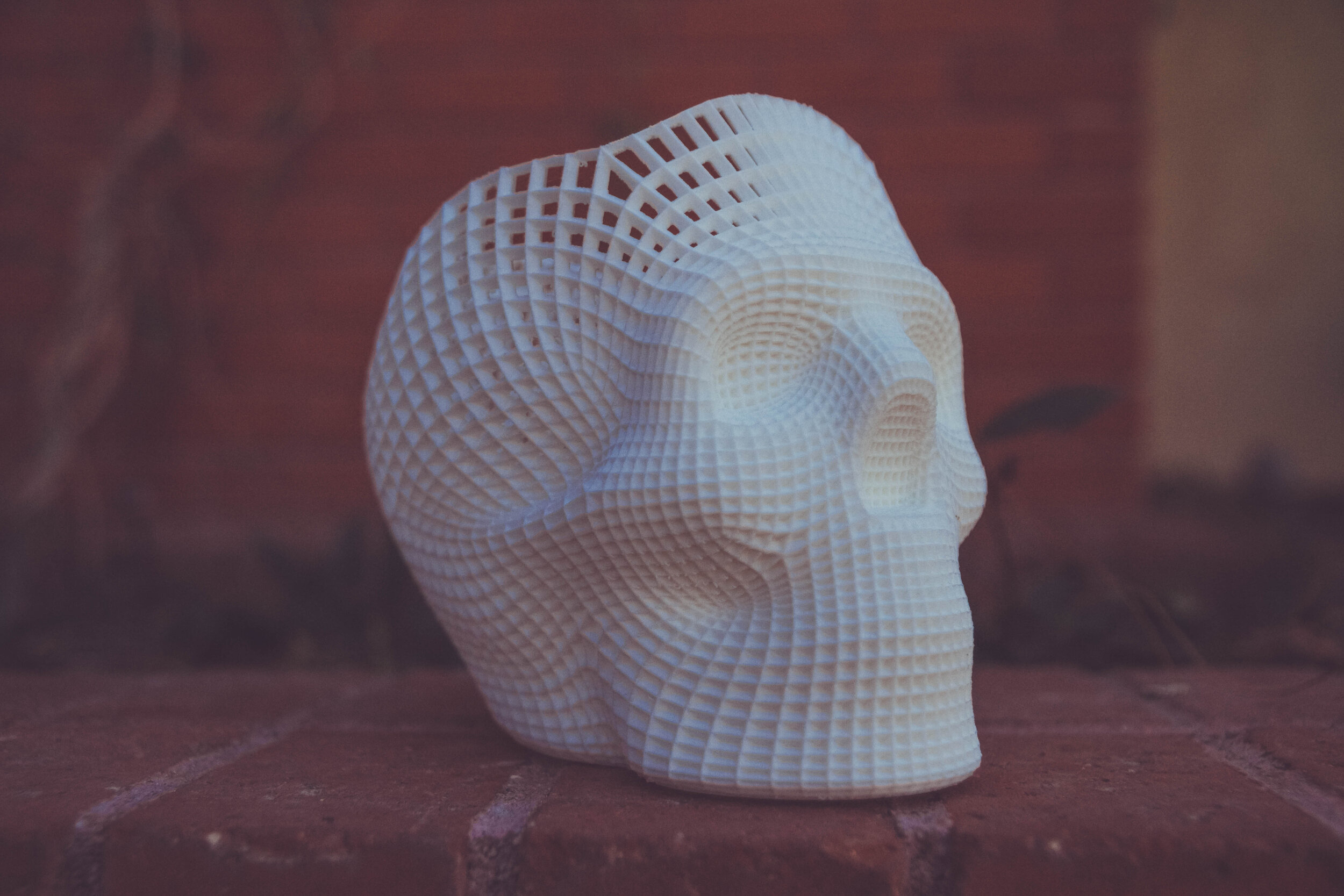